Maschinenthermometer: Alles was Sie wissen müssen
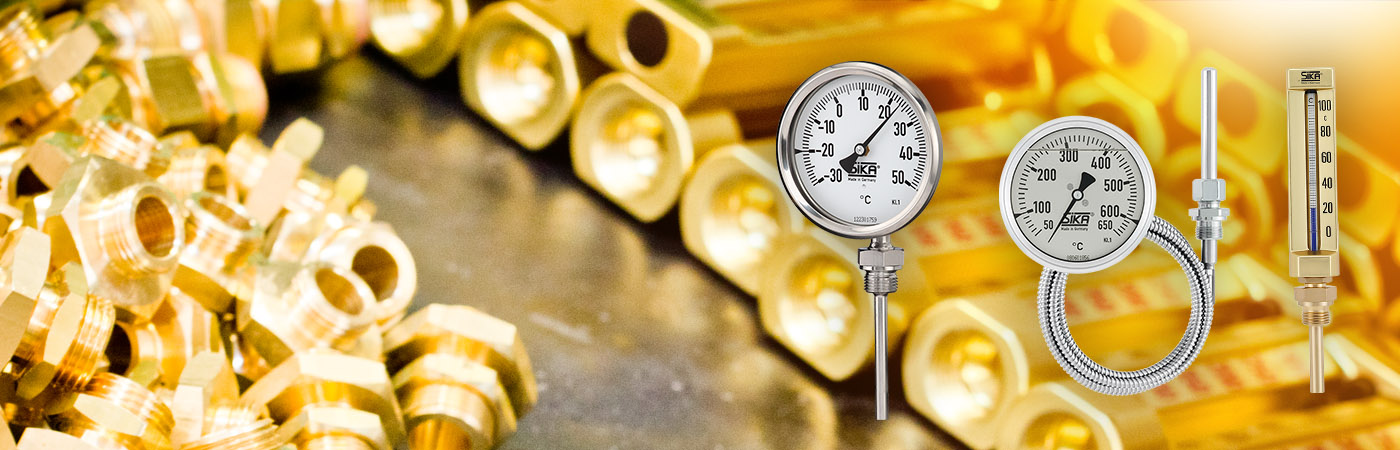
Unterschiedliche Typen von mechanischen Messgeräten werden zur Temperaturmessung verwendet. Besonders häufig werden Maschinenthermometer oder Zeigerthermometer z. B. in Heizungsanlagen oder auf Schiffen eingesetzt. Diese beiden Arten von mechanischen Thermometern werden in diesem Blogbeitrag detailliert vorgestellt. Sie erfahren mehr über die Entstehungsgeschichte des Maschinenthermometers, wie Maschinen- und Zeigerthermometer funktionieren und welche Vorteile ihr Einsatz mit sich bringt. Außerdem lernen Sie, warum Maschinenthermometer im Gegensatz zu anderen Messinstrumenten keine Kalibrierung benötigen. Was Sie beim Einbau von Maschinenthermometern und Zeigerthermometern beachten müssen, wird ebenfalls in diesem Beitrag erklärt. Abschließend werfen wir einen Blick auf die Frage, warum diese altbewährten mechanischen Messgeräte weiterhin ihre Berechtigung in der heutigen Industrie haben.
Wann und warum wurde das Maschinenthermometer erfunden?
Welche mechanischen Messprinzipien werden in unseren Thermometern verwendet?
Wie funktioniert ein Maschinenthermometer?
Welche Vorteile bietet der Einsatz von Maschinenthermometern?
Wie funktioniert ein gasgefülltes Zeigerthermometer?
Welchen Vorteil bietet die Verwendung von gasgefüllten Zeigerthermometern?
Wie funktioniert ein Bimetall-Zeigerthermometer?
Welchen Vorteil bietet die Verwendung von Bimetall-Zeigerthermometern?
Was sind die Gründe für die Kalibrierung von Messgeräten?
Warum müssen Maschinenthermometer nicht kalibriert werden?
Wie prüfen wir die Genauigkeit mechanischer Thermometer?
Was muss beim Einbau von Maschinenthermometern beachtet werden?
Was muss beim Einbau von gasgefüllten Zeigerthermometern beachtet werden?
Was muss beim Einbau von gasgefüllten Zeigerthermometern mit Fernleitung beachtet werden?
Was muss beim Einbau von Bimetall-Zeigerthermometern beachtet werden?
Wie werden Maschinenthermometer und Zeigerthermometer in die Anlage eingebaut?
Warum werden noch Maschinenthermometer und Zeigerthermometer verwendet?
Maschinenthermometer, genauer gesagt Maschinen-Glasthermometer mit V-förmigem Oberteil, sind eine Erfindung von SIKA.
Bis zu ihrer Erfindung, für die wir 1939 das Patent erhielten, waren Maschinenthermometer mit rundem Oberteil aus Messing und einer dünnen Kapillare auf einer Skala weit verbreitet. Kapillare und Skalenträger waren in einem Glasrohr eingeschlossen (sogenannte Einschlussthermometer). Sie ähnelten den Einkochthermometern, die viele vielleicht noch aus ihrer Jugend kennen.
Da Einschlussthermometer recht bruchanfällig waren, entwickelte Dipl.-Ing. Hans Siebert eine revolutionäre Konstruktion aus einer Vollmaterial-Stabkapillare. Die Skala wurde direkt auf die Stabkapillare aufgebracht und durch ein V-förmiges Gehäuse geschützt. Auf der Skalenwange des Gehäuses wurde der Messbereich eingraviert.
Diese Bauform zeigte sich im Marinebereich schnell als sehr erfolgreich, da sie wesentlich robuster war als ein Thermometer mit rundem Gehäuse.
In den Aufbaujahren nach dem Krieg wurde das SIKA Maschinenthermometer zunehmend auch im Anlagenbau eingesetzt und wurde in vielen großen Industriebetrieben in die Werksnorm aufgenommen. Die Industrie drängte daher bald darauf, unabhängig von einem einzigen Hersteller zu sein, und „überredete“ SIKA dazu, Maschinenthermometer mit V-förmigem Oberteil in eine DIN-Norm aufzunehmen. So rief Dipl.-Ing. Hans Siebert alle Mitbewerber zu einer Normungsbesprechung zusammen. Der Normungsprozess dauerte 10 Jahre und wurde 1962 abgeschlossen.
Beide Bauformen (rund und V-förmig) sind bis heute in der DIN 16195 zusammengefasst.
Unsere mechanischen Thermometer arbeiten nach dem Ausdehnungsprinzip. Früher wurden Maschinen-Glasthermometer mit Quecksilber gefüllt. Heute wird eine farbige Füllflüssigkeit auf Petroleumbasis oder Benzoesäure verwendet. Der Anstieg der Füllflüssigkeit in der Kapillare kann direkt am Glaseinsatz abgelesen werden.
Neben den SIKA Maschinenthermometern gibt es Zeigerthermometer, die entweder die Ausdehnung eines Gases im Messsystem (Stickstoff mit 5 % Helium) oder die unterschiedlichen Wärmeausdehnungskoeffizienten zweier Metalle in einer Bimetallwendel zur Messung nutzen. Bei Zeigerthermometern wird die Auslenkung der Rohrfeder oder des Bimetalls im Messsystem mechanisch auf ein Zeigerwerk übertragen.
Der Flüssigkeitsfaden in der Kapillare steigt oder fällt je nach Temperatur des Tauchrohrs. Das Maschinenthermometer misst über die gesamte Einbaulänge l1 und muss daher ausreichend tief in das zu messende Medium eintauchen. Der Einfluss der Umgebungstemperatur wird durch ein großes Gefäß (Reservoir für die Füllflüssigkeit) am Ende des Glaseinsatzes minimiert.
SIKA Maschinen-Glasthermometer haben eine lange Lebensdauer – problemlos bis hin zu mehreren Jahrzehnten.
Sie entsprechen den Anforderungen der DIN 16195 und werden während der Herstellung zu 100 % geprüft. Die Messgenauigkeit der SIKA Maschinen-Glasthermometer nach DIN 16195 wird von SIKA lebenslang garantiert (ausgenommen mechanischer Glasbruch oder Fadentrennung).
Sie unterliegen keiner Alterung oder Abnutzung und damit keinem Genauigkeitsverlust. Maschinenthermometer benötigen keine Fremdenergie und sind durch ihr Baukastensystem in vielen Kombinationen (Gehäuse, Messbereich, Einbaulänge, Gewinde, Tauchrohrwerkstoff) erhältlich.
Durch die Ausdehnung eines Gases im druckkonstanten Messsystem eines Gasdruck-Zeigerthermometers wird eine Rohrfeder im Gehäuse ausgelenkt, die ihrerseits ein mechanisches Werk bewegt. Dadurch ändert der Zeiger seine Stellung.
Der Einfluss der Umgebungstemperatur wird durch eine Bimetall-Kompensationsfeder minimiert.
Gasdruck-Zeigerthermometer sind die einzigen mechanischen Thermometer, die über eine Fernleitung an einer mehrere Meter entfernten Messstelle messen können.
Das Messsystem besteht aus einer Bimetallwendel, die aus zwei miteinander verbundenen Metallstreifen mit unterschiedlichen Wärmeausdehnungskoeffizienten besteht. Die dabei entstehende Bewegung (Auslenkung der Wendel) wird über eine Welle direkt auf einen Zeiger oder bei Winkelversionen über ein Winkelwerk auf den Zeiger übertragen.
Bimetall-Zeigerthermometer werden aufgrund ihres Messprinzips von Umgebungstemperaturen kaum beeinflusst, da die Temperatur nur Einfluss auf das Verhalten der Bimetallwendel hat
Die Gründe für die Kalibrierung von Messgeräten sind vielfältig. In verschiedenen Branchen gibt es Vorschriften wie ISO 9000, GMP, FDA, SOLAS, DIN, die eine regelmäßige Kalibrierung von elektronischen Temperaturmessgeräten und Temperaturfühlern vorschreiben. Damit soll die Genauigkeit der Messwerte sichergestellt und die Einhaltung von Qualitätsstandards gewährleistet werden.
Darüber hinaus können Messgeräte im Laufe der Zeit eine zunehmende Abweichung, auch Drift genannt, aufweisen. Diese kann durch verschiedene Einflüsse wie Vibrationen, Stürze, chemische Substanzen, Temperatur- und Druckänderungen, unterschiedliche Betriebstemperaturen, Feuchtigkeit, elektromagnetische Störungen, Verpolung und Kurzschluss verursacht werden. Eine regelmäßige Kalibrierung ermöglicht es, diese Drift zu erkennen und gegebenenfalls Korrekturen vorzunehmen, um die Messgenauigkeit wiederherzustellen.
Bei Maschinenthermometern gibt es keine Drift. Diese Thermometer behalten ihre einmal definierte Genauigkeit ein Leben lang. Die einzigen potenziellen Probleme können mechanische Beschädigungen des Glaseinsatzes oder eine Trennung der thermometrischen Füllung sein. Diese sind jedoch mit bloßem Auge sichtbar und können durch den Austausch des Glaseinsatzes oder die Wiedervereinigung des Fadens behoben werden. Eine unsichtbare, schleichende Drift wie bei anderen Messprinzipien tritt bei Maschinen-Glasthermometern nicht auf.
Die Herausforderungen beim Kalibrieren von Maschinenthermometern und Zeigerthermometern liegen in der spezifischen Konstruktion dieser mechanischen Messgeräte. Im Gegensatz zu Temperaturfühlern, die nur an der Fühlerspitze messen, messen diese Thermometer über die gesamte Einbaulänge l1 (Maschinenthermometer) bzw. über die aktive Länge des Kapillarbehälters (gasgefülltes Zeigerthermometer). Das bedeutet, dass die Umgebungstemperatur und die Abstrahlhitze des Gehäuses auch auf Teile der Kapillare wirken, die nicht im Medium eingetaucht sind. Diese Einflüsse werden durch die Konstruktion (z. B. Bimetall-Kompensation, Verhältnis Messmedienmenge Reservoir zu Kapillare usw.) und bei der Justage auf die für das Thermometer geforderte Genauigkeit minimiert.
Bei der Kalibrierung mit einem Trockenblock-Kalibrator muss die Länge des Kapillarbehälters berücksichtigt werden und die zusätzliche Messunsicherheit für die Kalibrierung angegeben werden. Somit könnten auch mechanische Thermometer mit einem Trockenblock-Kalibrator kalibriert werden. Dies erfordert jedoch umfangreiches Hintergrundwissen über die entstehende Messunsicherheit bei verschiedenen Einbaulängen l1.
Eine besondere Herausforderung besteht bei kurzen Einbaulängen von Maschinenthermometern (30, 40, 50, 63, 100 mm), da es nahezu unmöglich ist, die homogene Zone des Kalibrators (untere 40 mm des Kalibriereinsatzes) zu erreichen. Außerdem wird die Einbaulänge l1 ab dem Dichtbund gemessen, und das Gewinde ist Teil der Einbaulänge. Daher ist ein spezieller Kalibriereinsatz mit einer Stufenbohrung erforderlich.
Maschinen-Glasthermometer und Zeigerthermometer werden während der Herstellung mehreren Prüfungen unterzogen, um sicherzustellen, dass sie die vorgeschriebenen Genauigkeiten (DIN 16195 für Maschinenthermometer bzw. die verschiedenen Klassen für Zeigerthermometer) einhalten. Diese Prüfungen werden z. B. in gestoßenem Eis oder Wasserbädern durchgeführt.
Die Einbaulänge l1 sollte so weit wie möglich in den Prozess eintauchen, um eine genaue Messung zu ermöglichen. Die Einbaulänge wird vom Dichtbund einschließlich Gewinde bis zum Ende des Tauchrohres gemessen. Dadurch werden Abweichungen bei der Temperaturmessung vermieden.
Gasgefüllte Zeigerthermometer reagieren empfindlich auf Temperaturänderungen am Gehäuse (umgebungsbedingte Zusatzfehler). Um den Einfluss von Umgebungstemperaturen auf das Messergebnis zu minimieren, sollte die Umgebungstemperatur innerhalb der Referenztemperatur (23 °C ± 2 °C) gehalten werden. Gasgefüllte Zeigerthermometer sind so konstruiert, dass das aktive Gasvolumen (Gefäßinhalt) im Vergleich zum inaktiven Gasvolumen (Fernleitung und Messglied) sehr groß ist. Dadurch wird der Einfluss der Umgebungstemperatur auf das Messergebnis geringgehalten.
Der gesamte Temperaturfühler des gasgefüllten Zeigerthermometers sollte in das zu messende Medium eintauchen. Es muss unbedingt darauf geachtet werden, dass sich das Ausdehnungsgefäß mit seiner gesamten Länge ET vollständig im Medium befindet.
Die Temperatur am Gehäuse oder an der Fernleitung des gasgefüllten Zeigerthermometers mit Fernleitung sollte möglichst nahe an der Referenztemperatur (23 °C ± 2 °C) liegen, da sonst Zusatzfehler auftreten können.
Je länger die Fernleitung, desto größer muss das Gefäßvolumen sein. Unsere Datenblätter enthalten Richtwerte für die minimale Tauchrohrlänge, die aktive Länge ET und die Fernleitungslänge. Um den Einfluss der Umgebungstemperatur auf das Messergebnis zu minimieren, empfiehlt es sich, das aktive Gefäßvolumen größer zu wählen als das inaktive Gasvolumen, bestehend aus Fernleitung und Messglied. Bei Bedarf können Zeigerthermometer hergestellt werden, bei denen das Gefäßvolumen speziell auf den Anwendungsfall abgestimmt ist.
Die Fernleitung sollte nicht in der Nähe von Kälte- oder Wärmequellen verlegt werden, um eine Verfälschung der Messergebnisse zu vermeiden. Wenn die Fernleitung in der Nähe von Kälte- oder Wärmequellen vorbeigeführt werden muss, empfiehlt es sich, eine thermische Isolierung für die Fernleitung zu verwenden.
Bimetall-Zeigerthermometer sind unempfindlich gegenüber Umgebungstemperaturen, da sich die Temperatur nur auf die Bimetallwendel auswirkt. Sie können in einem Temperaturbereich von -40 bis 60 °C verwendet, transportiert und gelagert werden. Mit einer Gehäusefüllung können sie in einem Bereich von -20 bis 60 °C eingesetzt werden. Aufgrund ihrer Unempfindlichkeit gegenüber Umgebungstemperaturen eignen sich Bimetall-Zeigerthermometer auch für den Einsatz im Freien, z. B. bei direkter Sonneneinstrahlung.
SIKA Maschinenthermometer müssen immer mit dem Gehäuse senkrecht nach oben eingebaut werden, um eine Fadentrennung zu vermeiden. Der maximale Neigungswinkel beträgt 45°.
Die Einbaulänge l1 muss so tief wie möglich in das zu messende Medium eintauchen. Beim Einbau in Rohrleitungen gilt: l1 = min. ½ x Rohrdurchmesser
Das Tauchrohr sollte immer über die gesamte Länge vom Medium umspült werden, bei längeren Einbaulängen mindestens 2/3 der Einbaulänge. Die Justierlänge ist immer gleich l1.
Bei starken Beanspruchungen (Druck, Temperatur, Partikel) sollten zusätzliche Schutzrohre verwendet werden.
Zeigerthermometer müssen ebenfalls senkrecht eingebaut werden, insbesondere wenn sie mit einer Silikonölfüllung versehen sind, die das Zeigerwerk dämpft. Das Gasreservoir oder die Bimetallwendel (aktive Länge) muss vom Messmedium umspült werden, d. h. bei Einbau in eine Rohrleitung muss das Tauchrohr über die Rohrmitte hineinragen.
SIKA Maschinenthermometer haben eine sehr lange Lebensdauer – bis zu mehreren Jahrzehnten und ihre Messgenauigkeit entspricht den Anforderungen der DIN 16195.
Aufgrund ihres Messprinzips driften SIKA Maschinenthermometer nicht, da der Messeinsatz keine Verschleißteile enthält.
SIKA garantiert die Messgenauigkeit ein Leben lang – ausgenommen sind lediglich mechanischer Glasbruch oder Fadentrennung. Im Gegensatz zu anderen mechanischen oder elektronischen Thermometern unterliegen Maschinenthermometer praktisch keiner Alterung. Sie verlieren daher nicht an Messgenauigkeit.
Etwas anders verhält es sich bei Zeigerthermometern, da das Werk aus einer Vielzahl von Teilen besteht, die einem Verschleiß unterliegen, auch wenn das Thermometer zur Dämpfung mit Silikonöl gefüllt ist.
Im Gegensatz zu elektronischen Thermometern benötigen SIKA Maschinenthermometer und Zeigerthermometer keine Fremdenergie.
Selbst wenn die Stromversorgung komplett ausfällt, zeigen mechanische Thermometer noch zuverlässig Messwerte an. Dies ist insofern wichtig, als der Anlagenbetreiber im Störfall oder einem Anlagenstillstand einen schnellen Neustart gewährleisten muss. Zum Beispiel in einem Blockheizkraftwerk, das eine Gemeinde oder ein Krankenhaus versorgt, oder bei einem Blackout auf einem Schiff.
Darüber hinaus werden Anlagen routinemäßig begangen, um kleinere Leckagen oder Schmorstellen frühzeitig zu erkennen, wofür die menschlichen Sinne nach wie vor unverzichtbar sind.
Das Wartungs- und Instandhaltungspersonal nutzt dabei die Anzeigen vor Ort, zusätzlich zu den elektronischen Anzeigen am Leitstand oder auf dem Laptop.
Mechanische Thermometer werden aus Sicherheitsgründen als Backup zusätzlich zu den steuer- und regelbaren Messinstrumenten als fremdenergiefreie Vor-Ort-Anzeige eingebaut.
Wenn nicht mit zwei Messstellen gearbeitet werden soll, empfehlen wir eine Kombination aus Maschinenthermometer mit zusätzlichem Ausgangssignal – unser KombiTemp®.